Abstract
This paper aims to provide a guideline with respect to a reproducible thermal transient measurement for SiC MOSFETs. Although the thermal transient measurement based on sourcedrain voltage is a widely applied method for characterizing the thermal properties of MOSFETs, the approach developed for silicon-based devices may not be directly applicable to SiC devices. Therefore, this paper investigates the thermal transient measurement method for SiC MOSFETs using the source-drain voltage as the temperature-sensitive electrical parameter.
A comprehensive investigation of its linearity, sensitivity, and stability toward yielding the thermal structure-property of the device has been carried out. The investigation includes two primary characterization procedures: temperature calibration and cooling curve measurement. The associated key testing conditions, such as gate voltages, sensing and heating currents, etc., are covered. The study examines the impact of these conditions on both static and dynamic performance to provide a better understanding of the reproducible thermal transient measurement for SiC MOSFETs.
I. Introduction
Silicon carbide (SiC) MOSFETs are becoming increasingly popular in a wide range of applications, such as electric vehicles, industrial drives, and high-voltage transmissions. SiC offers several advantages over silicon, including lower power losses at higher switching frequencies, higher operating temperatures, and withstanding higher voltages. However, to ensure safe operation and maximize the device’s lifetime, all these superior performances must be achieved within the maximum junction temperature limit. Therefore, thermal characterization of SiC MOSFETs is essential to define the boundaries.
Thermal transient measurement is a widely accepted method to characterize the thermal properties of silicon (Si) power semiconductor devices. It has been recognized in several standards, such as JEDEC JESD 51-1 and JEDEC 51-14 and successfully applied to different applications over the past two decades, such as generating RC thermal models for electro-thermal simulation, packaging defect inspection, and junction-to-case thermal resistance measurement.
However, directly applying this approach to SiC MOSFETs is still doubtful to some extent. For instance, SiC MOSFETs do not have a pn junction in the forward direction and have low on-state resistance, which imposes challenges to measure transient thermal response by the channel voltage. Meanwhile, trapped charge carriers in the gate region may cause second-level electrical disturbances and inevitably affect the extraction of thermal transient from the coupled electrical disturbance. In the state-of-the-art, the source-drain voltage is one of the most used temperature sensitivity electrical parameters (TSEP) for SiC MOSFETs.
As shown in Fig. 1, the characterization consists of two major procedures, namely temperature calibration and cooling curve measurement. Improper selection of test conditions may result in misleading results. First, calibrating SiC MOSFETs for thermal transient measurement involves selecting the appropriate sensing current and gate voltage as step 1 shown in Fig. 1. While a sensing current of 1/1000 of the nominal current is commonly used for Si devices, it is however still under debate for SiC MOSFETs. Some studies use a small current below 1/1000 of the nominal current, while others suggest a much higher sensing current.
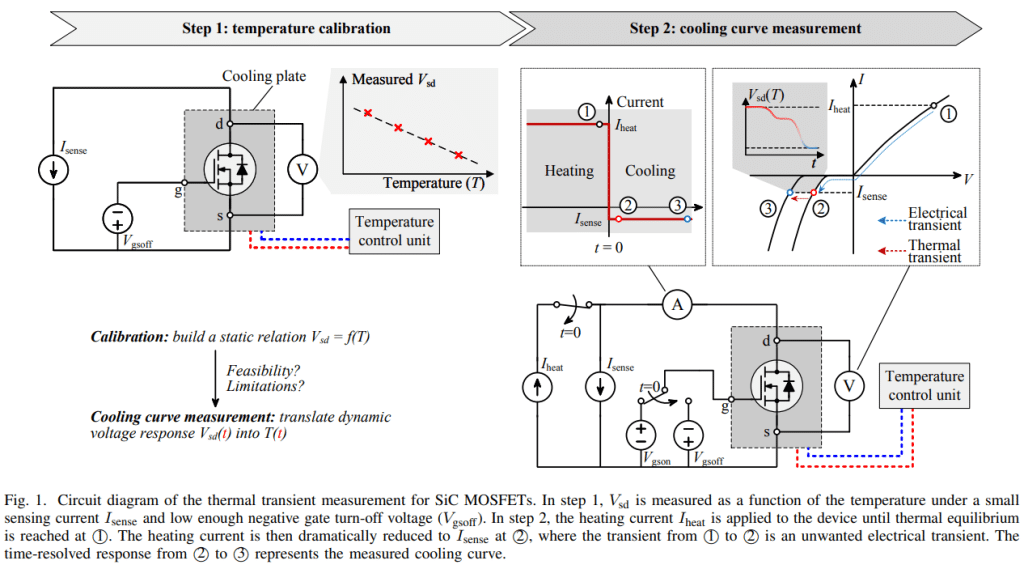
Additionally, selecting the appropriate negative gate voltage is critical for fully turning off the MOSFET channel and allowing all injected sensing current to flow through the body diode. However, the methodology for selecting the optimal gate voltage value and its impact on the transient thermal impedance remains unclear. It is worth noting that previous studies have mainly focused on steady-state calibration results, but transient temperature measurement requires consideration of transient behaviors, which has not been fully addressed in the literature. In addition to the calibration procedure, the cooling curve measurement of SiC MOSFETs involves other parameters such as heating currents and the switching transient of the gate state.
Previous studies have mainly focused on power cycling, where only the maximum and minimum temperature points are required. However, the investigation of thermal transient measurement with respect to the temperature dynamics across multiple time scales is limited. Electrical disturbances that occur at any point in time may lead to inaccurate thermal structure properties. Therefore, further investigation of the cooling curve measurement is also crucial. This paper comprehensively investigates the thermal transient measurement approach of SiC MOSFETs using Vsd as the TSEP and focuses on how to obtain more reproducible thermal structural information. Comparing to a preliminary conference version, the contributions of this article are three folds:
- Evaluated the impact of key testing conditions, including the gate turn-off voltage and sensing current, on the calibration based on static and dynamic tests. Three criteria are proposed to quantify the sensing current and two methods are proposed to justify the gate voltage.
- Investigated how various parameters affect cooling curve measurement in terms of static and dynamic responses.
- Derived a guideline of how to perform a reproducible thermal transient measurement of SiC MOSFETs with a proper selection of testing conditions and parameters.
II. Thermal Transient Measurement
Fig.1 illustrates the two major steps to perform the thermal transient measurement for a SiC MOSFET, namely, the temperature calibration and cooling curve measurement. The calibration is to obtain the relationship between the TSEP and the device temperature, which is controlled by an external system (e.g., an oven, a dielectric bath, or a temperature-controlled cooling plate). The MOSFET body diode pn junction voltage Vsd shows a linear temperature dependence given a small sensing current going through the device. By measuring Vsd under various temperatures, the relation of Vsd = f(T) can be calibrated.
Note that a low enough negative gate voltage has to be applied to completely shut the MOSFET channel off during this process (see Fig.2). In the second step, cooling curve measurement is carried out based on two current levels: one is the heating current (Iheat) to heat the device up, and the other is the sensing current for temperature monitoring with a negligible self-heating impact, as shown in Fig. 1 (Step 2).
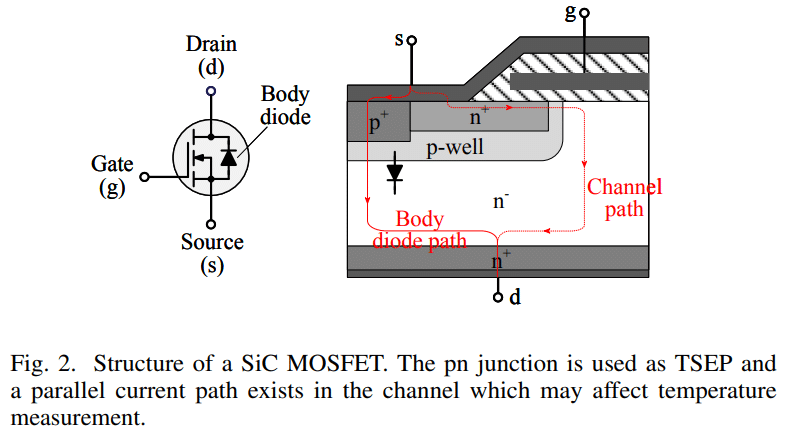
Once Vsd is measured, the inversely calibrated T = f−1 (Vsd) in step 1 converts the measured voltage into the temperature. However, the temperature calibration is developed based on static conditions but the cooling curve is derived from dynamic voltage responses. The compatibility of the two steps has a prerequisite that the electrical disturbance is short and negligible. However, reference pointed out that SiC MOSFETs have much longer electrical disturbance compared to Si devices. Its impacts on thermal transient measurement are not fully understood and will be investigated in the following two sections.
III. Calibration: Impact of Sensing Current
To obtain reliable thermal transient measurement for SiC MOSFETs, the sensing current needs to be carefully selected to achieve good linearity, sensitivity, and low power dissipation. Additionally, to minimize unwanted electrical disturbances, a short sensing current pulse is preferable. In this section, three criteria are proposed to quantify the impacts of sensing current.
A. Impact of Sensing Current Density on Static Performance
1) Linearity: pn-junction voltage Vpn is used as TSEP due to its linear temperature dependence, which is given by

where Eg is band gap, q is the elementary charge, kb is Boltzmann constant, and A is a device-specific factor. These parameters are either independent of or have weak dependence on temperature. When a constant sensing current density jsense is applied, Vpn varies linearly with temperature T. However, for SiC MOSFETs, the voltage drops across the drift region, contact, and metallization can contribute significantly to Vsd when a high sensing current is used.
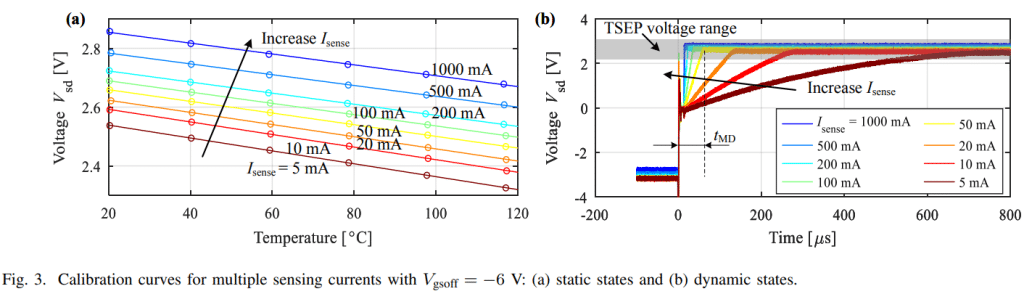
Moreover, at high temperatures and low current densities, the negative temperature coefficient of body diode results in a smaller Vpn. All above phenomenon can jeopardize the linear temperature dependence of Vsd and needs to be properly dealt. Fig. 3(a) shows the calibration results for different sensing currents ranging from 5 mA to 1000 mA. The proper selection of sensing current can be justified by the linearity between Vsd and temperature, which is further assessed by Pearson correlation coefficient ρlinear with 1 indicating perfect linearity

where cov denotes the covariance, and σ is the standard deviation. The left part of Table I lists that a sensing current of Isense = 100 mA gives the best linearity, whereas smaller and larger sensing currents result in a slightly worse performance.
2) Sensitivity: A viable TSEP sampling hardware requires a sensitivity SVT above 1 mV/K, which is defined as

Given a constant sensing current density, the temperature derivative of (1) yields

It indicates that when Vpn dominates the device’s voltage drop, the sensitivity decreases with the sensing current due to its negative logarithmic dependency in (4) and is also validated in the left part of Table I. All scenarios listed in the table meet the 1 mV/K requirement. Note that a higher or a lower SVT can also be selected according to the specific acquisition system.

3) Self Dissipation: To ensure accurate junction temperature measurement in the cooling phase, the self heating effect of the sensing current shall be negligible. A self-dissipation ratio is defined as

where Psense is the power dissipated by the sensing current which is generated by the measured TSEP voltage Vsd@Isense under Isense. Prate is the rated power dissipation of the tested device provided in datasheet. Generally, Prate can cause more than 100 ◦C junction temperature increase. ηsd ≤ 1% implies that the temperature increase by the sensing current is less than 1 ◦C (regarded as negligible here). Table I shows, except the cases of 500 mA and 1000 mA, all other scenarios meet the requirement of ηsd ≤ 1%.
B. Impact of Sensing Current Density on Dynamic Performance
During the period from 1 to 2 in Fig. 1, electrical and thermal transients occur simultaneously. This coupling poses challenge to extract the correct cooling curve of power devices. To address this issue, the standard JESD 51-1 introduces a delay time (tMD) to remove unwanted electrical transients plus a linear extrapolation to estimate the temperature at t = 0 s.
However, SiC MOSFETs are likely to suffer from long tMD, e.g., more than 600 µs under Isense = 5 mA in Fig. 3(b). It is much longer than the time scale of the chip’s thermal transient and hinders getting an accurate thermal structure property. However, by increasing Isense to 100 mA, tMD reduces to an acceptable 42 µs. Further increasing the sensing current has a limited effect on reducing tMD but rapidly increases the self-dissipation ratio.
Taking both static and dynamic performances into account, a sensing current of 100 mA achieves better overall performance for this study case.
IV. Calibration: Impact of Gate Voltage
A. Gate Turn-Off Voltage Selection
TCAD simulation in Fig. 4 shows that the electronic density changes dramatically in the channel region when the gate voltage varies from 0 V to -4 V but remains steady for a gate voltage less than -6 V to fully turn the channel off. This behavior is fundamentally different from Si devices, where a gate voltage of 0 V is sufficient as shown in Fig. 5(a).
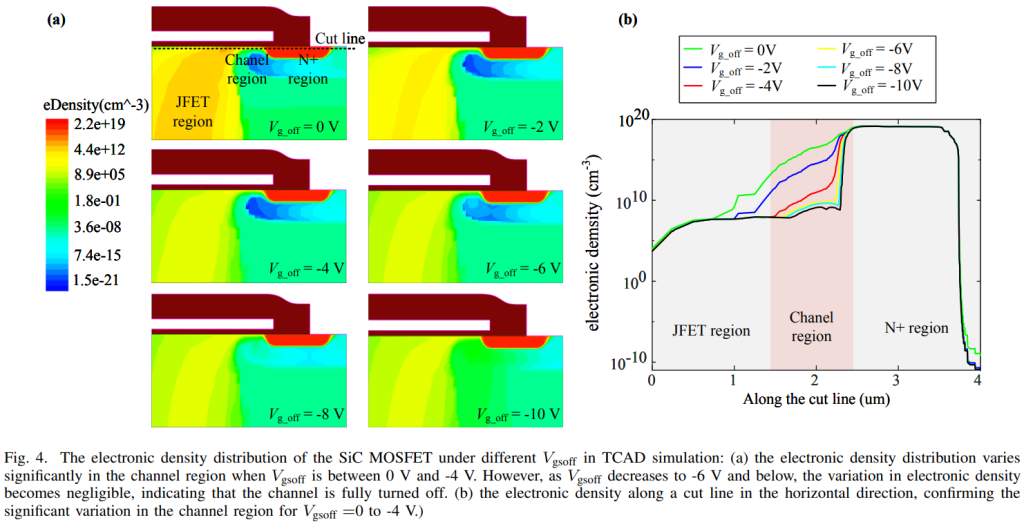

Although existing studies have experimentally shown that Vgsoff = −6 V is enough to turn off the channel of SiC MOSFETs, it may not be applicable to all SiC MOSFETs due to different die designs and manufacturing processes. Different devices will be discussed in Section VI-C and the following part will focus on two methods for gate turn-off voltage selection.
1) Method 1 – Output Characteristic under Sensing Current: Output characteristic curves of body diode under the sensing current range can shift significantly from each other in case of insufficient gate voltages, such as Vgs = −3 V in Fig. 5(b) but start to overlap as the gate voltage approaches -6 V. To quantify this effects, an electrical conductance gdiode at the sensing current is defined as
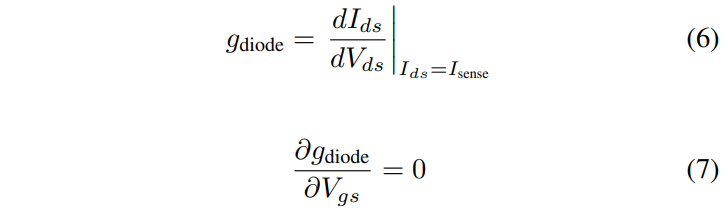
When the entire current flows through the internal body diode, the conductance is independent of gate voltage and becomes a constant. The minimum Vgs ensuring a completely-off channel can then be identified by (7), for example, Vgs = −4.5 V for this case study as shown in Fig. 5(c).
2) Method 2 – Calibration Curves with Varied Gate Voltages: The calibration curves show the relationship between the sensing current and TSEP, and shall overlap with each other under various gate voltage provided a fully turned-off MOSFET channel. At the meantime, TSEP is linearly dependent on temperature. Therefore, similar to method 1, the criteria defined in (8) can be introduced to identify the minimum reasonable gate tun off voltage, which is a slightly different Vgs < −5 V than Vgs < −4.5 V as shown in Fig. 5(d).

B. Static and Dynamic Impacts of Gate Voltages
The calibration results under various gate voltage are also evaluated with respect to the linearity, sensitivity, and self-dissipation ratio. The measured results and its analytical summary are show in Fig. 5(d) and the right-hand side of Table I. When the gate voltage changes from 0 V to -3 V, the linearity deteriorates significantly compared to the other gate voltages. This poor linearity indicates that the measured Vsd is not primarily determined by the pn junction.
Moreover, by adjusting the gate turn-off voltage from 0 V to -8 V, the sensitivity and the self-dissipation ratio changes minorly. Regarding the dynamic behavior, the time delays under varied turn-on and turn-off gate voltages are investigated in Figs. 5(f) and (g), respectively. The effect of the gate voltage on the measurement delay time is almost negligible. Within the device’s maximum allowable gate voltage range, a lower gate turn-off voltage can improve the static behavior without significantly affecting the dynamic performance of the thermal transient measurement.
V. Cooling Curve Measurement
Once the calibration is completed, the established relationship between Vsd and temperature can be utilized for cooling curve measurements, where the selection and impacts of heating current, gate turn-on voltage etc. will be evaluated.
A. Impact of Sensing Current
Fig. 6(a) shows the cooling curves of a SiC MOSFET under same test conditions except the sensing current. Ideally, the two measurements shall overlap completely. However, the case with Isense = 5 mA takes 663 µs to reach the state 2 , comparing to only 42 µs under Isense = 100 mA. This is due to the fact that the body diode requires sufficient minority carrier charge accumulation to turn on, and it takes longer for a smaller sensing current.
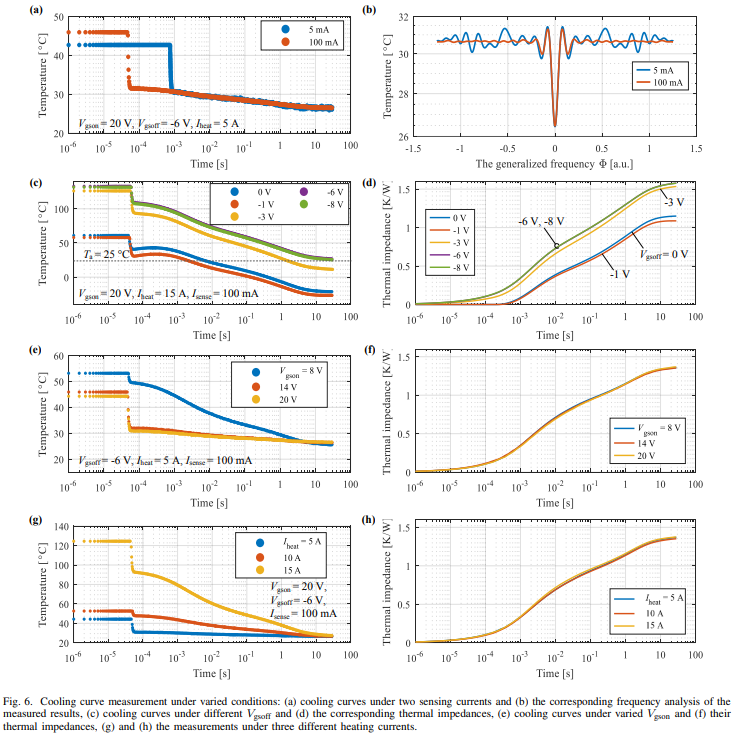
The above measurements validate the dynamic study in Section III-B. Furthermore, the frequency analysis in Fig. 6(b) shows measurements with Isense = 5 mA exhibit large high-frequency noises, while it decays rapidly when Isense = 100 mA. At a certain bandwidth ∆f of the measurement, the noise can be modeled as a Johnson-Nyquist form, that is,

where Rpn is the resistance of the body diode at Isense, i.e., Rpn ≈ kbT /qIsense. It indicates that the noise in the measured voltage diminishes with the square root of the sensing current. Thus, a higher sensing current is advantageous for both shorter electric transients and lower noise.
B. Impact of Gate Turn-Off Voltage
Fig. 6 c) illustrates a series of cooling curves measured under various gate voltages. (Note that each cooling measurement shares the same gate voltage with its used calibration curve, which can be found in Table I). Abnormal temperature rises at approximately 2×10−4 s can be observed with severely insufficient gate voltages (e.g., 0 V and -1 V) but disappears with gate voltages less than -3 V.
This phenomenon is inconsistent with physical principles as the cooling stage does not involve any heat injection and therefore junction temperature rise shall not appear. Similar behavior is also observed with a conclusion of imperfect SiC MOSFET structure. Another reason for this inconsistency can be the insufficient gate turn-off voltage based on above findings. Moreover, temperature measurements go below the ambient temperature of 25 ◦C for voltages less than -3 V but turn normal by further lowering voltage to -6 V and beyond.
Similar effects can be observed in Fig. 6(d) where the thermal impedance curves, reflecting the thermal structure of a semiconductor package, remains unchanged until the sufficient enough gate voltage is applied. These inconsistencies underscore the significance of the gate turn-off voltage.
C. Impact of Gate Turn-On Voltage and Heating Current
Gate turn-on voltage decides the channel voltage drop in the heating stage. Together with the heating current, a higher power dissipation results in a higher junction temperature. A maximum temperature difference of up to 20 ◦C and 80 ◦C are observed in Fig. 6(e) and (g) for different Vgson and Iheat. The derived thermal impedance curves, however, barely change as shown in Fig. 6(f) and (h). Additionally, the measurement delay time remains unchanged. Thus, conclusion can be made that Vgson and Iheat have negligible affect on the thermal characterization given a sufficient gate turn-off voltage and sensing current.
VI. A Guideline for Reproducible Transient Thermal Measurements of SiC MOSFETs
A. Junction-to-Case Thermal Impedance Measurement
Cooling curve measurement evaluates the thermal impedance from the device junction temperature to the ambient. More importantly, it can be used to identify the junction-to-case thermal impedance, which attracts more industrial interest. The JESD 51-14 standard clearly states the procedure by using transient dual interface approach. The overall principle is to conduct two transient thermal measurements of the identical device but with and without thermal interface material (denoted as tim and dry, respectively).
The two derived thermal curves start to separate as soon as the heat flow enters the TIM layer due to the surface roughness between package and cold-plate. Same procedure is followed in this paper based on the testing platform in Fig. 7(a) and previously identified test conditions of Vgs_off = -6 V and Isense = 100 mA. Subsequently, the cooling curves and thermal impedance curves are obtained as shown in Fig. 7(b) and (c). A clear separation point, or namely junction-to-case thermal impedance, can be observed at 0.8 K/W in Fig. 7(c) and in the thermal structure function curve in Fig. 7(d).

B. Transient Thermal Measurement Guideline
Based on the analysis and results discussed earlier, a flowchart to achieve a reproducible transient thermal measurement is provided in Fig. 8. It is evident that the gate turn-off voltage (Vgsoff) is a critical parameter that needs to be determined initially. Method 1 or 2 from Section IV-A can be applied. Certain margin can be added within the maximum gate voltage too as it benefits both static and dynamic states.
Subsequently, the sensing current (Isense) should be carefully selected. Too large or small sensing currents may not be conducive to accurate transient thermal measurements. It is important to ensure that the pn-junction dominates the measured drain-source voltage (Vsd) in terms of linearity, sensitivity, self-dissipation ratio, and measurement delay. Both the static and dynamic states should be evaluated comprehensively.

Once Vgsoff and Isense have been determined, the cooling curve measurement can be conducted accordingly. A final validation process can be added by varying the heating current (Iheat) or gate turn-on voltage (Vgsoff) to further validate the accuracy and reproducibility of the measurements.
C. Viability Validation
To validate the viability of the proposed flow, three additional devices from different vendors are tested with key information listed in Table II. Device 1 has been investigated in Section IV-V in detail. Fig. 9 shows the results of determining Vgsoff based on method 2. It is apparent that Vgsoff = −6 V, employed by multiple existing studies, is not sufficient enough for device 3 and 4 that require -10 V and -13 V to turn their channel off completely.
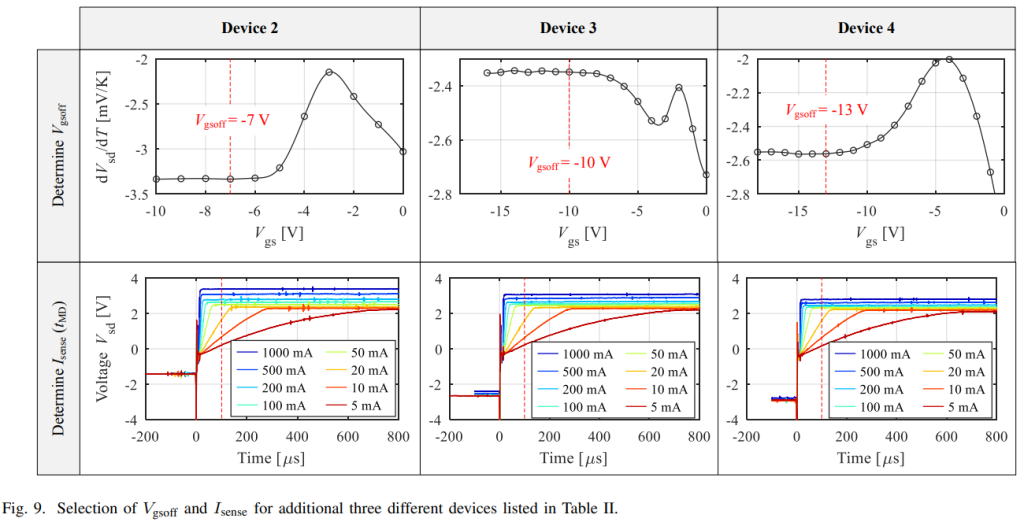
But it should be noted that these two values exceed the maximum allowable gate voltages according to devices data sheet. It implies that the current thermal transient measurement method based on Vsd may not be applicable to device 3 and 4 without exceeding the maximum gate turn-off voltage. Moreover, the selection of Isense with respect to the dynamic performance can be found in Fig. 9 together with the corresponding static performances listed in Table II. 100 mA is a proper sensing current for all 4 devices due to the short tMD and negligible self dissipation. It should be noted that the sensing current is around 5.26 ‰ of the rated current of the SiC MOSFET, which is different from Si devices.

VII. Conclusion
This paper investigates the thermal characterization of SiC MOSFET based on the body diode source-drain voltage. Two key steps, namely the calibration and cooling curve measurement, are evaluated comprehensively. The selection of key testing conditions, i.e., sensing/heating currents, gate turn-off/turn-on voltages, are thoroughly assessed based on their impacts on the thermal characterization and the following conclusions are achieved:
- Low enough gate turn-off voltage shall be used in both calibration and cooling curve measurement to ensure a completely shut channel and correct thermal impedance measurement. However, the required negative gate voltage may exceed the maximum allowable range, which causes the current thermal transient measurement method based on Vsd being not available for these devices within the maximum allowable gate voltage.
- Insufficient sensing current deteriorates the dynamics in terms of longer electrical disturbance and more noises, while too large sensing current sacrifices the steady-state performance in particular of a large self dissipation ratio.
- Gate turn-on voltage and heating current have negligible impacts on the measured thermal impedance. The consistency of the thermal impedance under varied gate turn-on voltage or heating current can be used as a validation.
Besides, a guide flowchart to perform reproducible transient thermal measurement for SiC MOSFETs is provided in this paper, which includes the selection of the electrical parameters and a validation process.
Authors
Yi Zhang, Yichi Zhang, Zhiliang Xu, Zhongxu Wang, Voon Hon Wong, Zhebie Lu, Antonio Caruso
Original – Research Gate